It’s finaly moving…
Now i need to understand how Mach3 do the setup…
Looks great. Nice and fast, too.
I run mach3 on my mill. I could try to answer questions if you have them.
Thanks
I was on EMC2 (LinuxCNC) on my other cnc.
But i know nothing to setup Mach3.
How do you get the right value in Motor setup to have the relation to the reality… like moving in gcode 10mm is 10mm move in real… (trying to explain in english… lol)
I forgot how big that thing is. I could design a massive pullpull controlled hexapod and you could cut me an 18 servo pullpull case? Lol
It might be hard to explain exactly, I’m not at home at the moment and don’t remember where everything is in Mach3. I’ll try and if I’m wrong I’ll correct it when I get home tonight.
Under the setup tab, make sure that the machine is set for mm (you use metric right?), in the lower left hand corner I believe.
Then, to figure out the value to put in the ‘steps per’ box in the motor tuning and setup window follow these steps:
You’ll need the pitch of your lead screws (travel per rotation, let’s call that P), the microstep setting from your servo drivers (call that M) and the number of full steps your steppers are capable of ( usually 200 per rev, call that F). Steps per = F/M/P.
For example, I use lead screws with 8mm pitch, set my drivers to 1/10 microstep and my steppers are 200 full steps per rev. So Steps per = 200/(1/10)/8 --> 200/(1/10) = 2000 and 2000/8 =250. Meaning it takes 250 microsteps to move 1mm.
Let me know if this helps.
Thanks… i will try all that… i have see the setup now.
I think my controller is at 1/8 microstep… what do you recommend ?
Did you guy ever see that:
vhipe.com/product-private/SuperPID.htm
hmmm well, not really good choice for CNC mill router. better to buy chinese water or air cooled spindle with inverter, more silent and muuuch more precise than that.
i would say ELTE or Jaeger or Kolombo or Perske whatever else than this hand mill be better but these names are too expensive for hobby CNC
Well my Bosch Colt was precise enough for me on the old CNC.
Just not strong enough for the new one.
I will put a set of Precision Collet just like i did on the Colt.
Hey Dialfonzo, if you tell me what the pitch of your leadscrews is I’ll calculate it for you. Then, if you have a dial indicator, I can show you how you can precisely calibrate your leadscrews. That’s not totally necessary though.
And the router will prob be good for cutting g10 and stuff but if you’d like to get into molding then I’d agree with Zacharius. You’ll want your TIR to be as low as possible to keep clean walls on your molds. But either way, I can’t wait to see that thing running. It looks pretty awesome.
Link for a dial indicator: amazon.com/Dial-Indicator-Ma … +indicator
How low we are talking about?
I am looking tu buy a SuperPID variator at some point.
Will get me around 5000rpm.
Thanks i think i will order the dial indicator.
I am not sure of the pitch right now (yes… Must ask the seller)
They are Thompson 2510 if i remember right.
Yes i am setup in mm.
Here is the cnczone thread
cnczone.com/forums/xzero_cnc … 40x48.html
Thanks all for your help
So I couldn’t find specific specs on the thomson ballscrews but Im guessing the 2510 means 25mm Diameter and 10mm lead. So try 160 for the ‘steps per’ box for your x and y axes. If your z screw looks the same as the y then put 160 in for that too. And I’d suggest starting with accels around 150 for your x and y, maybe 200 for the z. The z won’t be so crucial but you don’t want to the weight of the carriage to make your cuts wobble by accelerating and stopping too fast. That things looks really rigid though so you can probably bump up the accel after experimenting a bit.
What would you recommend the settint to be … on the driver ?
The microstep setting
You could be alright with 1/8. That’ll give you a resolution of .00625mm. If you have the option to go to 1/16, and they’re decent drivers, then you might as well. For that option you’d have to set your ‘steps per’ to 320 but you’d have a resolution of .003125mm. A steps per of 160 is for the 1/8 option.
Those look pretty nice. I would try the 1/25 microstep, I don’t see a reason to go any higher than that. If you use that then set your ‘steps per’ value to 500.
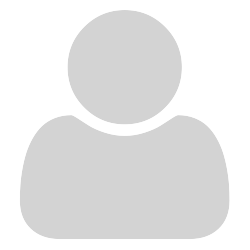
Those look pretty nice. I would try the 1/25 microstep, I don’t see a reason to go any higher than that. If you use that then set your ‘steps per’ value to 500.
Ok i will try that…
(if only i could buy time…)
On my current CNC i have it at 1/8 i think. It’s a Xylotex all in one driver
Ok here is a printscreen of the motor tuning for 1/25 micro stepping.
Am i right… ? (lol)
Couple of question… i have found that with the arrow key i can Jog, but where do i set the jog speed…?
The GCode load screen (3d view of toolpath) is strange.
Can’t see it really good… is it normal… ?
I have buy a screenset … the original is pretty ugly… and compare to LinuxCNC
DiaLFonZo - Pocket-Test.zip (2.61 KB)
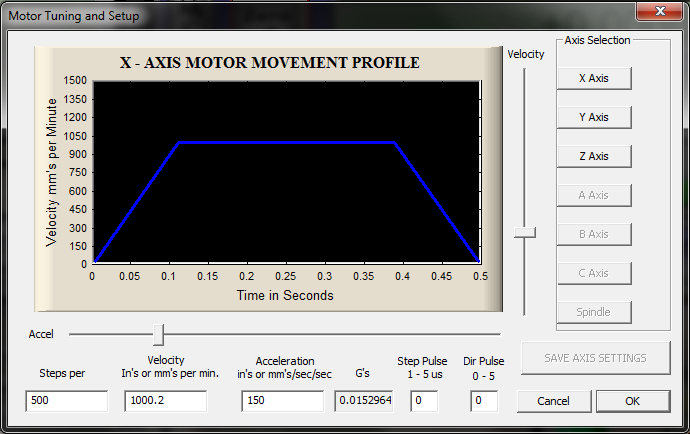
With those settings… when i jog it move very slowly
Ok… let’s say…
1/16 microstep
200 step per turn
10mm pitch
Steps per = 200(1/16)/10
2000/8 = 250
so in the case Step Per in motor setup i put 250… right ?