What is a Robotic Manipulator?
Robots are used in science and industry to replace or entertain humans and although they do not have to look like us nor have to perform tasks in a humane manner, many of them do. In fact, some of the most popular in the industry are robot manipulators which resemble the human arm.
Robot arms are designed to manipulate and transport parts, tools, or special manufacturing elements through reprogrammable movements to perform a variety of tasks. This is why they are commonly used in industrial environments, although there are also scale versions dedicated to STEM education and hobby robotics.
Elements of a Robotic Arm
The mechanism of a robot manipulator consists of the articulated mechanical structure and the end-effector. The end-effector constitutes the interface with which the robot interacts with its environment, so it can be any device intended to manipulate objects (i.e. grippers and suction cups) or to transform them (i.e. laser engravers and 3D printing devices). The mechanical structure is composed of a kinematic chain constituted by a combination of links and joints. One end of the chain is fixed and is called the base and the end-effector is fixed to the free extremity of the chain.
The links are rigid members connecting the joints of the robotic manipulator and can be revolute or prismatic. They are considered revolute when they produce the relative displacement of two links joined by an axis (involves rotation between links), and prismatic when they produce the relative displacement of two links along an axis (linear motion).
An endless number of combinations can be created with these types of joints, and therefore there are many types of configurations.
Types of Robotic Arms
Some of the most popular configurations are:
Articulated/Revolute Robot (RRR) SCARA Robot (RRP) Parallel Robot
Cartesian Robot (PPP) Polar Robot (RRP) Cylindrical Robot (RPP)
And that's only using three joints! But robotic arms can have as many as needed. However, what really matters is not the number of joints but what they can achieve. This is where the term “Degrees of Freedom” comes in. In general, the term Degrees of Freedom (DOF) is used to describe the number of parameters needed to specify the spatial pose of a rigid body or system.
They are described as:
Translational
- Moving forward and backward on the X-axis. (Surge)
- Moving left and right on the Y-axis. (Sway)
- Moving up and down on the Z-axis. (Heave)
Rotational
- Tilting side to side on the X-axis. (Roll)
- Tilting forward and backward on the Y-axis. (Pitch)
- Turning left and right on the Z-axis. (Yaw)
In theory, in a mechanism or linkage containing a number of connected rigid bodies, such as a robotic manipulator, the degrees of freedom measure the combined positioning capability of the system. However, in practice, DOF is often referred to as the number of single-axis rotational joints in the arm, where a higher number indicates increased flexibility. This is why you may have seen that some robotic arms have more than 6 degrees of freedom.
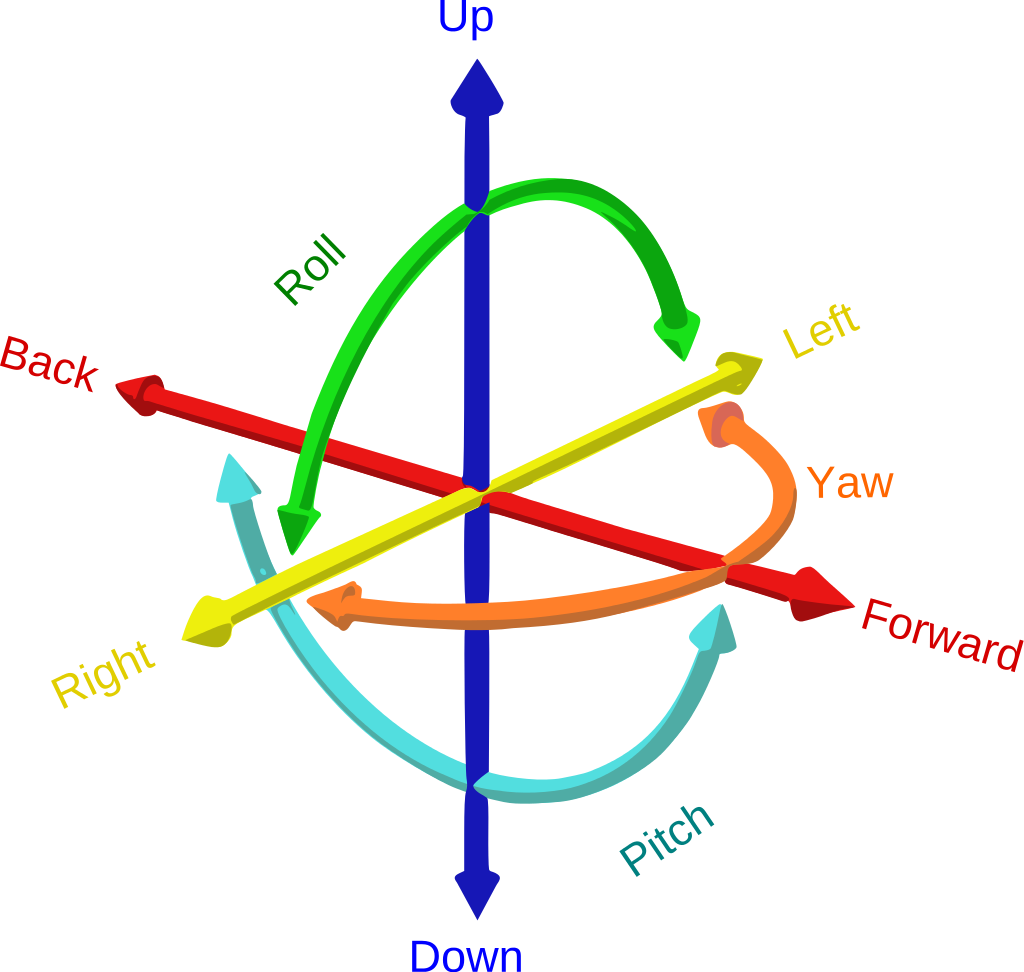
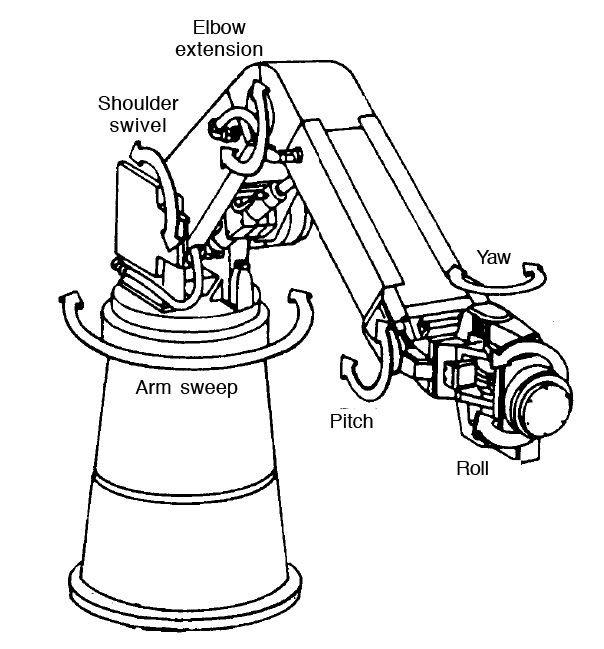
A robot that has mechanisms to control all 6 physical DOF is said to be holonomic. A robot with fewer controllable DOF than total DOF is said to be non-holonomic, and a robot with more controllable DOF than total DOF (such as the human arm which has 7 DOF) is said to be redundant.
Serial and parallel manipulator systems are generally designed to position an end-effector with 6 degrees of freedom. This provides a direct relationship between actuator positions and the configuration of the manipulator defined by its forward and inverse kinematics, which describe the actual arrangement of links and joints and determine the robot's possible motions, but we will further discuss this in the following tutorial. However, if you are planning on getting a robotic manipulator, but don’t know what you should be looking for, the following terms will also come in handy.
What to Look for When Choosing
- Number of axes: This is usually the same as the degrees of freedom. Two axes are required to reach any point in a plane; three axes are required to reach any point in space. To fully control the orientation of the end effector three more axes (yaw, pitch, and roll) are required.
- Payload: How much weight the robot can lift. This will vary according to the distance of the end-effector to the base so it is generally measured at the maximum horizontal reach of the arm which is the most demanding case.
- Speed: How fast the robot can position the end-effector. This depends on the speed of the motors used in the joints.
- Acceleration: How quickly an axis/joint can accelerate.
- Working envelope: This is the region of space a robot can reach.
- Accuracy: How closely a robot can reach a commanded position. This measurement is equal to the difference between the commanded position and the absolute position of the robot.
- Repeatability: How well the robot will return to a programmed position.
Although they seem very similar, accuracy and repeatability are different measurements. Repeatability is usually the most important for a robot and is similar to the concept of precision. To easily understand the difference here’s an example: when told to go to a certain position the arm could get only to within 2 mm of that position, this would be its accuracy which can be improved by calibration. However, if each time it is sent there it returns to within 0.2 mm of the position then the repeatability will be within 0.2 mm.
Those are some of the most important definitions when it comes to robot manipulators. However, if what you are looking for isn’t acquiring a robotic arm but building one then I suggest checking the How to Make a Robot Tutorial Series as well as the Robot Arm Torque Tutorial. And if you are looking for one but are still not sure where to start check out the Educational Robotic Arms, and the Semi-Professional Arms. Don't be shy to ask questions or contribute to the conversation in the replies to this post.