Andrew Fails to center a hole
I’m trying to make some couplers so I can connect the Mr. Basic drive shaft to a short length of steel cable. The goal is to create a flexible drive shaft.
Here’s the problem, I have so far consistently failed to get a hole drilled straight through the axis of a 1/4 inch steel rod.
Update 2009-09-28: Success! I had another blunder and then finally got it. I added pictures too.
Attempt #1:
- Used a Dremel to cut off and clean up an 8mm piece of steel rod. No problem.
- Center tapped “by eye” the end of the rod.
- Used a 3/32 inch drill in a drill press, with the rod held in a vice.
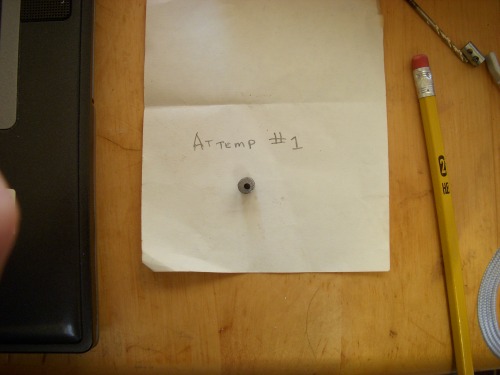
Result: The hole was visibly off-center.
Attempt #2:
- Used a Dremel to cut off and clean up a 5mm (which is too short, I forgot to double-check the required length) piece of steel rod.
- Tried a cute idea I read about on the web for a center tap jig. The result was WAAAY off center, so I went back to just visually centering and taping the end of the rod. I had to Dremel down the originally off-center tapped hole.
- Used a 3/32 inch drill in a drill press, with the rod held in a vice.
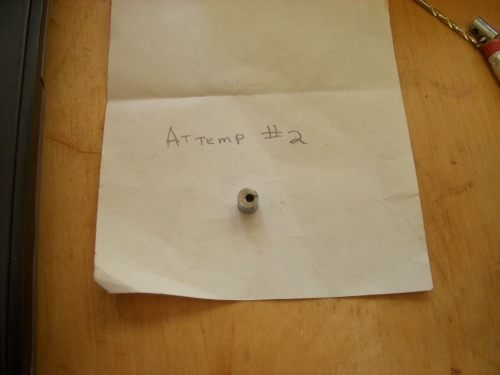
Result: The hole was off-center. The rod was too short.
Attempt #3 (a bit better):
- Cut and center tapped the piece as before.
- This time I really watch the drill as it started to cut, and I saw that even with the center-tapped hole, the bit tended to wander.
- I REALLLY slowed down the downward pressure, and let the hole establish itself in the center before pushing through.
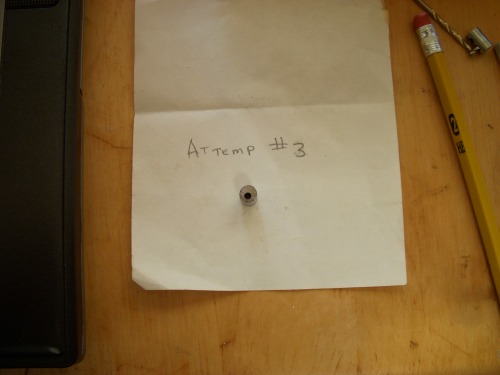
Result: The hole was centered on ONE SIDE, and off-center on the other. GRRRRRRR!
At least I'm learning. Next time I'll be 100% sure I have the piece in the vice vertically. I'll go slow all the way through the cut, and i'll try using some oil to lubricate the drill bit before cutting. I'll also double check the speed I'm running the drill press at.
Update!
Attempt #4 (Oh! The humanity!)
- Tried another one. It was still off-center, but at least the hole went straight through.
- Decided to try the two side holes for the set screws. Tight fit since the piece wound up about 7.5 mm long, and each hole is 3/32 (almost 2.5mm).
- Two side holes center-tapped, drilled, and threaded. OK!
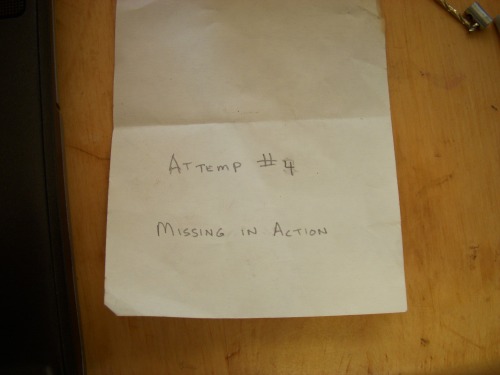
Result: Put in the set screws, but one got stuck and wouldn't back out. One half of the slotted head snapped off, and I can't get the f***er out even with vice grips. I ALMOST had it.
Attempt #5 (Busted drill bit!)
- This time I thought I had it.
- Everything was going so well.
- I got as far as drilling the hole for the last set screw and BAM! The piece went flying.
- I didn't have it clamped down well, and the tip of the drill bit snapped off!
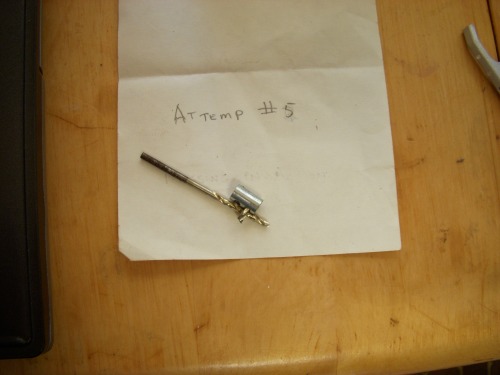
Result: Busted my nice shiny drill bit and had to substitute an old, not so sharp one.
Finally! Success!
- I was able to salvage the piece from attempt #5.
- Pausing only long enough to document my disaster, I got a new bit and this time rigged a good clamp.
- Everything came out swell.
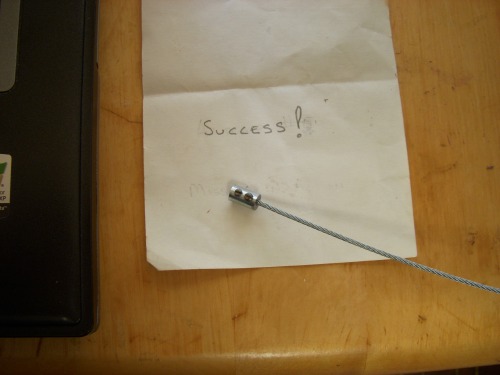
Result: Set screws are holding in the steel cable. Now I just need a 2.5mm drill bit so I can widen the center hole for the Mr. Basic drive shaft.
Oh, yeah... and build like seven more of these.
Learn well from my mistakes, oh reader.