Hey @ryangoc
The manufacturer doesn’t offer any plot/graph for reflective target vs range nor experimental data on LIDAR testing with Oil Surfaces.
I have found more information concerning your questions in the manufacturer’s FAQs:
How do distance, target size, aspect, and reflectivity effect returned signal strength?
The device transmits a focused infrared beam that reflects off of a target, and a portion of that reflected signal returns to the receiver. The distance is calculated by taking the difference between the moment of signal transmission to the moment of signal reception. Sucessfully receiving a reflected signal is heavily influenced by several factors. These factors include:
- Target Distance
The relationship of distance (D) to returned signal strength is an inverse square. So, with increase in distance, return signal strength decreases by 1/D^2 of the square root of the distance.
- Target Size
The relationship of a target’s Cross Section © to returned signal strength is an inverse power of four. The decice transmits a focused near-infrared laser beam that spreads at a rate of approximately 0.5° as distance inscreases. Up to 1m it is approximately the size of the lens. Beyond 1m, the approximate beam spread in degrees can be estimated by dividing the distance by 100, or ~8milliradians. When the beam overfills (is larger than) the target, the signal returned decreases by 1/C^4 or the fourth root of the target’s cross section.
- Aspect
The aspect of the target, or its orientation to the sensor, affects the observable cross section and, therefore, the amount of returned signal decreases as the aspect of the target varies from normal.
- Reflectivity
Reflectivity characteristics of the target’s surface also affect the amount of returned signal. In this case, we concern ourselves with reflectivity of near infrared wavelengths
In summary, a small target can be very difficult to detect if it is distant, poorly reflective, and its aspect is away from the normal. In such cases, the returned signal strength may be improved by attaching infrared reflectors to the target, increasing the size of the target, modifying its aspect, or reducing distance from the sensor.
How does the device work with reflective surfaces?
Reflective characteristics of an object’s surface can be divided into three categories (in the real world, a combination of characteristics is typically present):
- Diffuse Reflective
- Specular
- Retro-reflective
Diffuse Reflective Surfaces
Purely diffuse surfaces are found on materials that have a textured quality that causes reflected energy to disperse uniformly. This tendency results in a relatively predictable percentage of the dispersed laser energy finding its way back to the device. As a result, these materials tend to read very well.
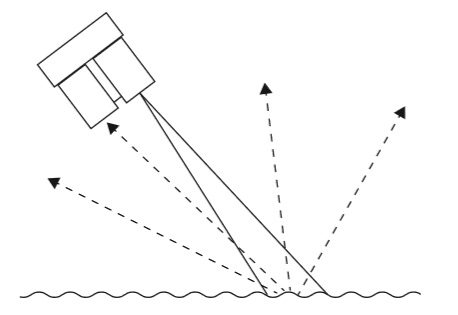
Materials that fall into this category are paper, matte walls, and granite. It is important to note that materials that fit into this category due to observed reflection at visible light wavelengths may exhibit unexpected results in other wavelengths. The near infrared range used by the device may detect them as nearly identical. For example, a black sheet of paper may reflect a nearly identical percentage of the infrared signal back to the receiver as a white sheet.
Specular Surfaces
Specular surfaces, are found on materials that have a smooth quality that reflect energy instead of dispersing it. It is difficult or impossible for the device to recognize the distance of many specular surfaces. Reflections off of specular surfaces tend to reflect with little dispersion which causes the reflected beam to remain small and, if not reflected directly back to the receiver, to miss the receiver altogether. The device may fail to detect a specular object in front of it unless viewed from the normal.
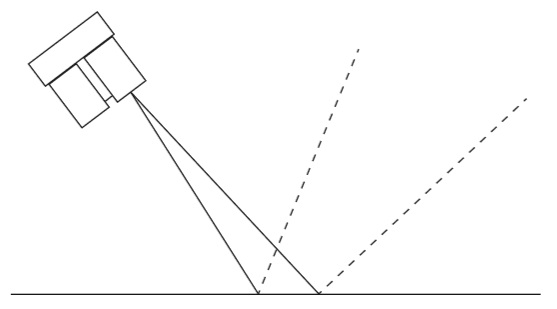
Examples of specular surfaces are mirrors and glass viewed off-axis.
How does liquid affect the signal?
There are a few considerations to take into account if your application requires measuring distances to, or within, liquid:
- Reflectivity and other characteristics of the liquid itself
- Reflectivity characteristics of particles suspended in the liquid
- Turbidity
- Refractive characteristics of the liquid
Reflectivity of the liquid is important when measuring distance to the surface of a liquid or if measuring through liquid to the bottom of a container. It is important to note that measuring distance with the device depends on reflected energy from the transmitted signal being detected by the receiver in the sensor. For that reason, the surface condition of the liquid may play an important role in the overall reflectivity and detectability of the liquid. In the case of a flat, highly reflective liquid surface, the laser’s reflected energy may not disperse adequately to allow detection unless viewed from the normal. By constrast, small surface ripples may create enough dispersion of the reflected energy to allow detection of the liquid without the need to position the sensor so that the transmitted beam strikes the liquid’s surface from the normal.
Reflectivity of suspended particles is a characteristic that may help or hinder depending on the application.
Turbidity, or the clarity of a liquid created by the presence of absence of suspended particles, can similarly help or hinder measurement efforts. If the application requires detecting the surface of the liquid, the suspended particles may help by reflecting more on the transmitted beam back to the receiver, increasing detectability and permitting measurements to be taken.
It is important to note that, attempting to measure through suspensed particles in a liquid will only be successful if the transmitted beam is allowed to reflect off of the desired target without first being absorbed or reflected by the suspensed particles.
When the near infrared energy transmitted by the device transitions from the atmosphere to a liquid, the energy may be bent, or refracted, and absorbed in addition to being dispersed. The degree to which the transmitted beam is refracted and absorbed is defined by its refraction index. That being said, the most important criteria impacting successful measurement through a liquid is the amount of dispersion of the transmitted beam and whether any of the dispersed beam makes its way back to the receiver on the device.
Remember that electromagnetic energy travels slower through a liquid and may affect accuracy of the final measurement output.