To whom it may concern:
The link is shown as follows.
https://www.robotshop.com/en/catalogsearch/result/?q=force+sensor&order=relevance&dir=desc
I am working on piezoelectric materials. Piezoelectric materials can generate charge in response to mechanical input.
My setup can apply a pressure on the materials and I want to use the setup to calibrate the piezoelectric materials.
I need a reference sensor to measure the exact value of the force applied on the materials.
The maximum force that the setup can applied is 5N. Do you think the 10 N sensor is suitable for me to use?
Will the sensor be broken if I apply 12N force on the 10N sensor?
Thank you for your support.
Hello @Apple001forever and welcome to the community!
Could you please specify which sensor you’re referring to? Is it the following one?
In case the answer is yes, here’s the information you need:
The analog output swings from 0 to 2V, with the valid working output ranging from 0.5V to 1.5V as
shown in the Figure.
As pressure increases beyond the full scale range (FSR) the output will increase to 2V and then limit.
The sensor should be unloaded at power on to allow the sensor’s baseline to be registered correctly.
NOTE: An output below 0.5V may indicate negative pressures, which occur when the sensing area is
under tension. This should be avoided since it can damage the internal structure of the sensor.
NOTE: Sensor over pressure should be limited to less than 3x FSR to avoid damaging the sensor.
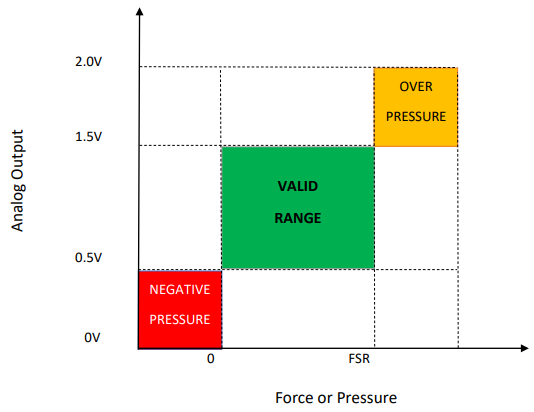
So if you use a 10N force sensor, 12N wouldn’t damage the device, but 30N would.
I’m not sure about how much precision you need for the calibration but SingleTact force sensors offer repeatability errors that are less than 1.0% of the FSR. So for a 10N sensor would be 0,1N but for a 4,5N would be 0,045N and you would need to apply a force of approx 13,5 to damage it.
I hope that information can help you out 