Have you wondered why some robots can run much longer than others, or why UAVs can only hover for a few minutes? The battery pack you choose is certainly important, but there are many additional factors which have a huge influence on the total time your robot operates between charges.
Drive Motors
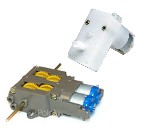
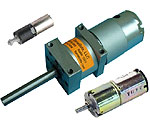
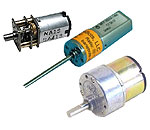
The drive motors you choose will be one of the most important factors affecting the operating time of your robot. You need to choose motors based on the required torque, rpm and operating voltage. A standard brushed motor might be 60% efficient, meaning that only 60% of the "power" provided by the battery is converted into rotational motion, and the other 40% is converted to heat (wasted). An efficient brushless motor can operate a7 95% efficiency, but such motors tend to be expensive.
Finding a motor that is 100% efficient is not possible. This means that 100% of the electricity supplied to the motor is converted into useful mechanical energy. Highly efficient motors are able to operate at 80-90% efficiency, but this is only under nominal conditions. An inefficient motor can even operate at 40% efficiency or less. Efficiency losses in motors can be attributed to heat, friction (bearings at both ends of the shaft are ideal), wind resistance (any motors have integrated cooling fans), coiling of the wires and control method. Some manufacturers are kind enough to include the graphs of efficiency versus voltage and rpm though others prefer not to make that information public.
Gearing
Gear downs are purely mechanical systems and as such are subject to wear and tear, friction, manufacturing defects and more. The more gears the system uses, the less efficient it will be. The most efficient type of (commonly available) gear down in the hobby market is planetary, followed by spur gears and then worm gears. Planetary gears are more efficient than spur and worm gears but tend to also be more expensive because they are harder to produce. A worm gear can greatly reduce the speed (and increase torque) in one stage, but is highly inefficient. A standard spur gear system can be 50% efficient, while a very efficient planetary gear system, properly lubricated, can be upwards of 80% efficient.
Battery Pack Voltage
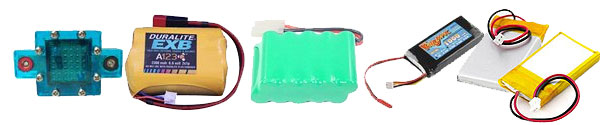
The voltage of the battery pack you choose should ideally be as close as possible to the nominal voltage of your main drive motors. For example if you are building a 2WD robot using two 6V nominal geared motors, then your battery pack should ideally be 6V as well. For example, if you are building a multi-rotor helicopter using motors operating at 11.1V, then your battery pack should ideally be 10.8 to 12V. If you operate a motor at above or below the nominal voltage, the motor runs less efficiently, converting more and more of the battery pack's stored energy to heat, reducing the time the robot operates. Below are popular battery types:
- 1.2V: One AA or AAA NiMh cell
- 1.5V: One Alkaline AA or AAA cell
- 2.4V: Two NiMh cells
- 3V: Two Alkaline cells
- 3.6V: Three NiMh cells (best for small DC gear motors such as Tamiya)
- 3.7V: One LiPo battery
- 4.8V: Four NiMh cells (minimum voltage for powering
- 6V: Four Alkaline cells
- 6V: Five NiMh cells (best for hobby servo motors and small DC gear motors)
- 7.2V: Six NiMh cells
- 7.4V: Two LiPo cells (need a voltage regulator if you want to power servos)
- 7.5V: Five Alkaline cells
- 8.4V: 7x NiMh cells
- 9V: 6x Alkaline cells
- 9.6V: 7x NiMh cells (good for powering DC gear motors and the microcontroller from one battery)
- 10.5V: 7x 1.5V cells
- 10.8V: 9x NiMh cells
- 11.1V: Three LiPo cells (best for robots requiring a light weight ~12V power supply, ex. helicopter).
- 12V: 10x NiMh cells (best for small / mid sized mobile robots using 12V DC gear motors)
Most rechargeable battery packs are never fully recharged; they oxidize or lose capacity over time. A perfect battery might be able to retain over 99% of its charge over a large number of cycles, though a less efficient pack might lose 0.5% or more per recharge. NiCd are being used less and less because of what is called the "memory effect"; if the battery is not properly drained, it will be hard to recharge to its full capacity.
Battery Pack Capacity
The capacity of the battery pack (measured in Amp Hours) has a direct impact on the total time your robot will operate between charges. Keep in mind that if you want the robot to operate for a long time, your battery pack will either be heavier or offer a higher capacity for the same size (using a different chemistry).
Terrain
The type of terrain encountered by the robot plays a huge role on the current required by the motors and therefore greatly impacts the time a robot will operate. A robot moving at a steady speed on a horizontal surface will last a lot longer than a robot moving up a 30 degree incline. Rough terrain (outdoors) is unpredictable and rarely flat.
Common Operating Times
The following is simply a reference to give you an idea of how long might can expect a properly configured robot will last:
- Small (indoor) wheeled robot: 30 minutes to 2 hours
- Medium sized (outdoor) wheeled robot: ~1 hour is common.
- Large wheeled robots: 30min to several hours
- Multi-rotor: 10-30 minutes
- UAV (aircraft): 1 hour +
- Humanoid robot: ~30 min
A 2000mAH ( = 2.0 AH) battery pack can power a robot with two drive motors drawing 1A each continuously for up to 1 hour. Similarly, it can power a robot with two drive wheels each consuming 0.5A for 2 hours (0.5 * 2 * 2). Usually, higher capacity battery packs are physically larger.
An important note is that battery packs rated at a specific capacity are not always intended to be used at the maximum discharge rate. For example, a battery pack rated at 5AH should not necessarily be discharged at 5A for 1 hour. It is suggest to add 20 to 40 percent extra capacity whenever possible, so if your project requires 5A continuously, you should select a pack rated at 5AH * 1.4 = 7AH. Remember to always check the rated peak discharge rate as motors that are starting up consume significantly more current (around stall current) when starting than when in operation.
No electromechanical system (which includes robots) is perfect and there will always be losses in efficiency. These losses can arise in many different areas, the most common of which are below:
Heat
Friction dissipates energy wherever moving parts are concerned. This includes the motor, gear down and wheels. This value is very difficult to calculate or measure. Friction losses are usually coupled with heat losses, though friction can also include wear and tear and losses in material due to grinding action.
Losses due to heat can occur almost everywhere in a robot. The area on a robot where the most heat is lost tends to be the motor controller, especially when the motor is subjected to a heavy load. Many motor controllers are sold with a heat sink to quickly dissipate the heat, and heat sinks are highly suggested if the controller does not come with one. However, this does not stop the total energy loss but rather lowers the temperature of microchip and H-bridge faster. If your robot is going to encounter situations where a lot of energy will be expended (such as an inclined surface, lifting weights or others), then it is best to consider a maximum of 80% efficiency. However, if your robot is moving on a flat surface, and the motors and motor controller you selected are properly matched to the robot's weight and specifications, then you might consider 90 to 100% efficiency.
Calculating Efficiency
Efficiencies are multiplied, not added; if you consider the efficiency of the motors, gear down and motor controller to be 80%, 85% and 75% respectively, the overall efficiency of the system will be:
0.8 * 0.85 * 0.75 = 0.51 = 51% overall efficiency.
When you design your robot, make sure to include losses in efficiency, otherwise your robot will not perform as you expected. The following are estimates of efficiency to help you calculate your robot's overall efficiency, though you should check the product's user guide to see if the manufacturer provided the efficiency:
- Hobby DC Brushed Motors: 70%
- Hobby DC Gearing: 3% loss per stage
- NiMh Battery discharging at nominal V: 65%
- LiPo Battery discharging at nominal V: 85%
- Hobby DC Motor controller: 65 - 90%
- Microcontroller: 90%+