I’m looking at the picture and I don’t see a rotary socket. I do see a nut that you can loosen to rotate the vise however. Regardless the rotary vise, you do great work!
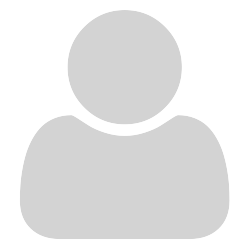
I’ve never seen one of those before. At my highschool machine shop we have a CAM that is guided by computer software in which you design your cut-out on. Is this a manual way of doing that (as in without the computer aided software)?
No computers, total manual. They managed to create fine mechanical parts before 1960’s too
Hi Joe,
Yes, that’s a real drill/mill! That’s all my HS shop class had.
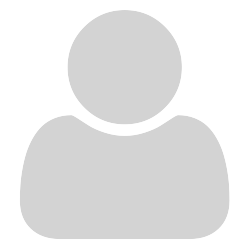
I’ve never seen one of those before. At my highschool machine shop we have a CAM that is guided by computer software in which you design your cut-out on. Is this a manual way of doing that (as in without the computer aided software)?
CAM is “Computer Aided Manufacturing”, you first draw your part in CAD, then generate a tool path (for the mill or torch to follow), and then generate Gcode with the CAM software. The Gcode is then sent out (carried out, “sneaker net”) to the mill, and the part program (Gcode) is run. If you got the code right, then you get a nice, shiny part; if not…
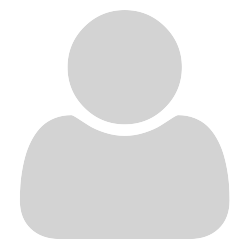
Yes, you do see a arc… Laughing
It’s quite easy. The vise has a rotary socket. Take a closer look at the picture Wink
Yeah, I was staring at the part apparently being cut, and missed (until I looked again) at the OBVIOUS part laying in the foreground!
I’ve used such tricks in the past to cut parts, but I much prefer my current CNC methods (lazy).
Alan KM6VV
CAM is “Computer Aided Manufacturing”, you first draw your part in CAD, then generate a tool path (for the mill or torch to follow), and then generate Gcode with the CAM software. The Gcode is then sent out (carried out, “sneaker net”) to the mill, and the part program (Gcode) is run. If you got the code right, then you get a nice, shiny part; if not…
Yup, I just wasn’t sure how you manufacture the parts with that. I thought it was a stationairy bit. I didnt know you had to move the machine manually. Such skill to get those parts perfect.
Looking forward to seeing the doc’s for the spreadsheet.
Hi Jim! Check your email…
Thanks! Can we put this on the website yet?
Thanks! Can we put this on the website yet?
Of course! I’ll send you updates as soon as I have done some more documentation.
I have the Phoenix project page up on our website now - sorry for taking so long!
The PEP spreadsheet program and manual are available for download through the links on the project page. I’ve started a new topic for discussion of the PEP here:
lynxmotion.net/viewtopic.php?t=3117
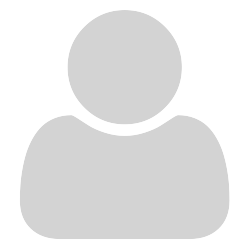
Yup, I just wasn’t sure how you manufacture the parts with that. I thought it was a stationairy bit. I didnt know you had to move the machine manually. Such skill to get those parts perfect.
You don’t have to move the tool manually. It can be (and should be) a fully automated and computer controlled process. My Alibre Design Expert has a new AlibreCAM module that can generate g-code code directly for a CNC machine or other package such as Visual Mill or SprutCAM. Unforunately, I can’t afford and don’t have any place to put a CNC machine. It would be wonderful to be able to mill my own parts (and PCBs).
8-Dale
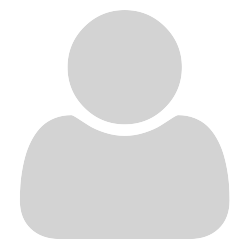
Yeah! those are only the cost of a nice laptop! I might get one in the future.
I have a Sherline CNC mill, and they cost more than that. The reason they do is you have to buy a pile of accessories before it really becomes useful - hold down clamps, milling vise, etc.
What I did was buy this package:
sherlinedirect.com/index.cfm … uct_ID=745
And then picked up a 3-axis control system:
xylotex.com/Econo3AxSpecial.htm
I use Mach3, which is an excellent control package.
I hooked it up to an old 1 GHz P3 system (laptop) I have running XP, and it works great…
- Jon
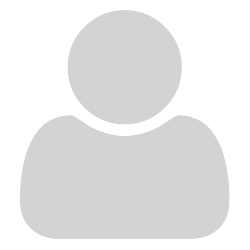
I have a Sherline CNC mill, and they cost more than that. The reason they do is you have to buy a pile of accessories before it really becomes useful - hold down clamps, milling vise, etc.
What I did was buy this package:
sherlinedirect.com/index.cfm … uct_ID=745
And then picked up a 3-axis control system:
xylotex.com/Econo3AxSpecial.htm
I use Mach3, which is an excellent control package.
I hooked it up to an old 1 GHz P3 system (laptop) I have running XP, and it works great…
- Jon
True, after all the accessories, I can imagine it costing a little more but the base system is very reasonable considering its a CNC machine. I was looking at the Smithy Granite machines and after you add CNC control, it costs over $6,000.
Jon, how “rigid” is the sherline? I imagine it has to cut slower due to its power. I saw some examples on their website and was impressed with what it can do. That turbo prop was cool!
The Sherline is rigid enough to do the small stuff we need for building robots. I cut plastic, aluminum, and brass typically. People who are real machinists cut stainless steel with them, but I’m nowhere near the level of precision or patience required to do that.
It really depends on what you’re trying to cut. For small legged robots, you have to use lightweight materials like Delrin or Sintra, and you can cut fairly fast. The mini-sumo I’m building now is mostly aluminum and brass, so it takes a little longer.
To give an example, it took about 3 hours each to machine one wheel and one motor mount:
- Jon
The Sherline mill and lathe are good little machines. I have CNC’d both of mine (my own CNC control program), and routinely make parts for my working model steam engines.
http://www.marconettengineering.com/BeamEngineFinished11B.jpg
http://www.marconettengineering.com/TinyTangye2B.jpg
I design the parts with Vector CAD/CAM, generate the Gcode, and then run my CNC Controller program to read the Gcode and run the stepper motors running the mill or lathe. Fun! I can cut a lot of shapes (curves) that I couldn’t otherwise cut conveniently, if at all. Nature has curves, Biomimetic robots need curves!
The Sherline mills and lathes are rigid enough (you can never get all the rigidity you want) to mill plastics, brass, aluminum and steel, if you take it slowly. Accuracy is pretty good, you get what you pay for; don’t expect them to perform like $30,000 USD tool room mills/lathes!
I’ve also just made the two body plates for my now-working hexapod robot, and you’ve seen the proposed octapod robot body plate. All machined on my CNC’d Sherline mill, although obviously they are too big for the 4" x 8" work envelope of the mill. The answer is to do the machining in two or more setups with a fixture. This gave me an effective 8" x 8" work envelope needed to machine my plates.
Dale has emailed me his new WALTER deck plate designs (4 decks, whew!) which are 11.5" octagons with wheel cutouts on the lowest deck, and servo horn hole patters on the remaining 3 decks. I will need 4 setups and a new fixture to do his, and then I’ll still have to manually drill the center cluster of holes (can’t reach 'em) on a larger (RF-31) bench mill. I think Dale will be posting some rendered 3D drawings of his decks over on the WALTER thread.
Check out the Sherline list on yahoo, or my SherlineCNC list below.
Alan KM6VV
Hat’s off to you sir. Very clean and nice work on the steam engine.
I have a mini lathe in the shed, and maybe I’ll be adding a mini mill to it this weekend, but unfortunately I don’t have the skills (yet) to get such smooth clean parts from them.
Just out of curiosity, have you learned the trade somewhere (work/school) or did you learn by yourself?
Alan,
Great job on the engine! I want a Sherline! Does vectercad have a demo program that I can try out? Also, are you using MachIII?
Hi,
Thanks for the kind words! I must say I’m quite proud of them and the others I’ve built.
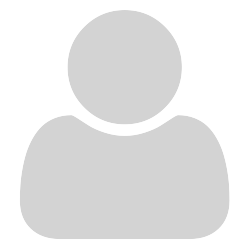
:shock: Hat’s off to you sir. Very clean and nice work on the steam engine.
I have a mini lathe in the shed, and maybe I’ll be adding a mini mill to it this weekend, but unfortunately I don’t have the skills (yet) to get such smooth clean parts from them.
Just out of curiosity, have you learned the trade somewhere (work/school) or did you learn by yourself?
Congrats on your budding machine shop! I think you’ll enjoy it. I get a lot of enjoyment out of designing and building such mechanical things. Hardware and software as well.
I mostly taught myself, I did take a shop class eons ago in HS. Also ran the lathe on the submarine I was on (USS James Monroe SSBN622), and on the submarine tender when we were tied up alongside.
Then my wife gave me first a lathe and then a mill for birthday/Christmas/etc. How did she know I wanted them? ;>)
I found the bits for CNC by searching the web; and learned much on the Yahoo lists. The information is out there!
Alan KM6VV
Hi Mike,
Thanks!
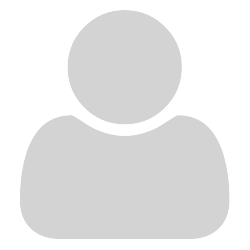
Alan,
Great job on the engine! :shock: I want a Sherline! Does vectercad have a demo program that I can try out? Also, are you using MachIII?
Vector CAD/CAM DOES have a time-limited demo. Tell Fred I sent you!
I have Mach 3; which is quite good, and recommended, however I have the CNC Control program (STEP4) that I wrote that I am quite comfortable with, and can add/change/improve whenever I want. So I do all my machining with it.
I think Mach 3 demos also. Art is a pretty good guy.
Alan KM6VV
I have actually downloaded and tried out the Mach3 program months ago, and I also watched the excellent tutorial video.
Since I don’t have a mill, I was not sure how it worked with the machine.
I will give VecterCam a spin.