Here is an image of the progress so far. The hardware aspect is going great. The parts are ordered. The electronics from the open servo folks, not so well. They are having trouble getting the spec’d current from the H-bridges. Not sure how it’s going to pan out just yet.
Jim Honestly, thats awsome!
Thanks Joe! 8)
Wow, that is really cool! I can’t wait to order a few of those. Hopefully the OpenServo project will pan out. I ordered some OpenServo hardware and am planning on playing with some of the motors as well. Thanks for the update and all your hard work!
Chris
Sweet,and phooohhee to all the naysayers
Not to worry, as of this afternoon the rest of the OpenServo team is on the case. The ‘couple of OpenServo guys’ Jim ‘hired’ are wearing sack cloth, eating only stale bread and flogging themselves three times a day for the duration.
Look for working Open LynxServo boards sometime in the next 2-3 weeks.
Cliff
Jim,
Your picture of the brackets/motors looks nice, but I don’t understand how the servo boards mount. To make the motor responsive, the servo board needs to be close to the motor. Long cables are fine for driving wheels but not so good for driving servo motors. What’s the plan?
Cliff
Jim,
Another quick question, if you don’t mind.
In an earlier post, you stated that the motors used for this project were pghm04 and pghm05, which according to the spec. sheets are the same size. In your photo above, you show two different motor sizes - what is the smaller motor shown and do you have plans to use yet other motors for this product line?
Thanks in advance,
Cliff
I am eagerly looking forward to them! And I hope the sack cloths are not too uncomfortable, this is supposed to be a fun hobby and I’d hate to see anyone get chafed skin. Ground breaking pursuits such as these are bound to have their ups and downs. If it were easy everyone would be doing it! : )
Chris
If the pot has the same resistance range as in other servos with large motors, I’d use the guts from that servo to control the gearhead motors to start getting some run time on the new setup. I noticed the motors are 12v, which might have to be worked around. It would be good to have the gearhead set to run routines under load contineously for an extended period of time to detect any correctble issues early. With the absence of normal servo controls, simple limit switch setups could be used to exercise the arm for extended periods of time.
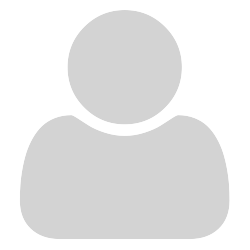
Not to worry, as of this afternoon the rest of the OpenServo team is on the case. The ‘couple of OpenServo guys’ Jim ‘hired’ are wearing sack cloth, eating only stale bread and flogging themselves three times a day for the duration.
Look for working Open LynxServo boards sometime in the next 2-3 weeks.
Ouch, that sounds painful!
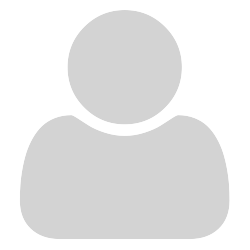
Your picture of the brackets/motors looks nice, but I don’t understand how the servo boards mount. To make the motor responsive, the servo board needs to be close to the motor. Long cables are fine for driving wheels but not so good for driving servo motors. What’s the plan?
The plan is to encapsulate the entire board in heatshrink as the model airplane folks are doing with their speed controllers. A little velcro / double sided tape / tiewraps should hold it in place well enough. We may do something a little nicer in the future.
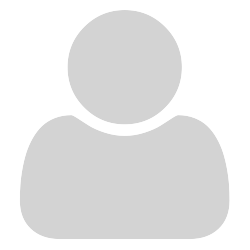
In an earlier post, you stated that the motors used for this project were pghm04 and pghm05, which according to the spec. sheets are the same size. In your photo above, you show two different motor sizes - what is the smaller motor shown and do you have plans to use yet other motors for this product line?
I may have chosen some part numbers that were used for different motors, I honestly don’t remember. The smaller 22mm motor is PGHM-04 but the larger 32mm motor is not on the website yet. I’m still experimenting with gear reduction. I hope to add a 25mm motor too. It would go to the elbow and the 22mm motor would move to the wrist. It’s all evolving, and everything looks very promising.
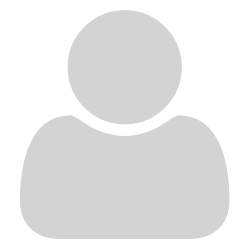
If the pot has the same resistance range as in other servos with large motors, I’d use the guts from that servo to control the gearhead motors to start getting some run time on the new setup. I noticed the motors are 12v, which might have to be worked around. It would be good to have the gearhead set to run routines under load contineously for an extended period of time to detect any correctble issues early. With the absence of normal servo controls, simple limit switch setups could be used to exercise the arm for extended periods of time.
I do have an order in for the HS5745MG guts. They will probably work under reduced loading to test the assembly. 12vdc operation will be a little bit of a hassle. But the increased performance should make it worth the trouble.
I do have an order in for the HS5745MG guts. They will probably work under reduced loading to test the assembly. 12vdc operation will be a little bit of a hassle. But the increased performance should make it worth the trouble.
That sounds very interesting. Can you post the results of your testing? Would it be possible for the lay-person to order the “guts” from somewhere?
Thanks,
Chris
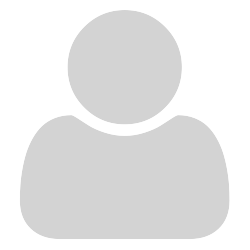
That sounds very interesting. Can you post the results of your testing? Would it be possible for the lay-person to order the “guts” from somewhere?
Thanks,
Chris
Yes I will post the results. As soon as they are received we will get them on the website. I expect the price to be around $15.00 to $17.00. 8)
I expect the price to be around $15.00 to $17.00. 8)
Excellent! I didn’t realize you were purchasing them for resale, so that’s even better! Thanks again : )
Chris
One could make a simple motor testing setup using parts from Radio Shack. The first link below has a drawing of a motor reversing setup using a toggle switch, diodes, and limit switches. The second link shows a simple way to use a servo to operate a the toggle switch, and the bottom links show the components that should be at the local Radio Shack store. Sould be easy to mount the arm components on a board and have the arm section swing the rated weight load overhead 180 deg. left/right to get some run time on the arm setup. If one really wanted to be inexpensive, the switches could be made from components usually found in the kitchen junk drawer.
geocities.com/zoomkat/switch.htm
geocities.com/zoomkat/t-stat.htm
tinyurl.com/yrh2ns
tinyurl.com/2eyobe
tinyurl.com/2fjqco
Hi all,
You don’t know me here, but I am part of the OpenServo team.
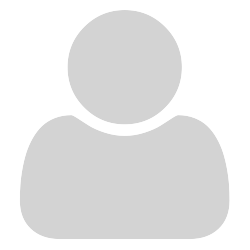
Not to worry, as of this afternoon the rest of the OpenServo team is on the case. The ‘couple of OpenServo guys’ Jim ‘hired’ are wearing sack cloth, eating only stale bread and flogging themselves three times a day for the duration.
Look for working Open LynxServo boards sometime in the next 2-3 weeks.
Cliff
Kinky!
I have been asked to participate in the creation of the LynxServo v2. I look forward to working with you all on this project. With the help of Cliff, and the rest of the OpenServo team, we should have some working hardware in no time at all.
The design process will all be available for all to read over at
(post restrictions lifted so I can put link in)
www.openservo.com/Forums/viewtopic.php?p=2912
Feel free to hop on over and comment.
Barry
New toys !!! hey guys i dont want to side track you but this is going to be like a pwm motorcontroller with a pot for position feed back , how hard would it be to make this regenarative ?? since the action of moving servos is so wastefull (accelerate decelarate ect…) cause with things we,r
gonna need some big batteries 8)
Hi cbradsmith,
Regenerative braking is pretty tricky, so I don’t think we are going to be able to squeeze this in. Maybe next revision
Barry
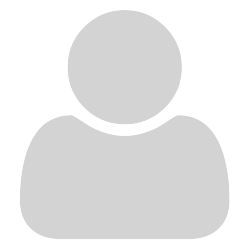
Hi cbradsmith,
Regenerative braking is pretty tricky, so I don’t think we are going to be able to squeeze this in. Maybe next revision
Barry
just an idea,would,nt help much with hex,s or arm,s but the bipeds would get a boost,
anyway “Great Job Guys” !!!