We never actually made the board. The SJ chip was at $25.00 and discounts were not too good so I passed on it. Not sure what the cost and discount is now though.
It kinda looks like a photo-shopped BB2 board
Too bad! I could use one now.
do you have any bare boards (or other project information)? I’d be interested.
the Soundgin chip sounds interesting, as well as adding a TTS256; although it might only work with the Speakjet.
Thanks!
Alan KM6VV
You could probably make your own using perf board. If you download the speakjet manual, it shows a simple schematic of a basic bare minimum circuit. I don’t remember what page it was on.
Hi Mike,
Yeah, I could wire it up alright. I’ve seen the chip docs. I could even isolation-mill a PCB. Just looking for something convenient, and not another PCB project!
Alan KM6VV
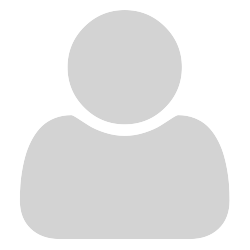
Hi Mike,
Yeah, I could wire it up alright. I’ve seen the chip docs. I could even isolation-mill a PCB. Just looking for something convenient, and not another PCB project!
Alan KM6VV
I hear ya! About your mill, what are you using? EMC2 what about the CAM software. I remember you mentioned all this before but I can’t remember what you said.
Hi Mike,
I use Vector CAD/CAM to post-process the Gcode generated from a user-added option to Eagle.
To run the mill, I use my own CNC controller program (STEP4 for mill and lathe).
Actually, I’m hoping to get a demo board for the SoundGin chip this Christmas! If not, I’ll either buy it myself, or mill a board.
Alan KM6VV
I have been manually machining parts and practicing using my milling machine. It is harder than I thought when trying to create accurate parts that need to be within .001" I tried counting hand wheel turns and I miscounted on one of the cuts and scraped the part. I found scribing lines was a lot easier. CNC is still my goal. I need a lot more practice with setups. Trying to figure out how to hold a part accurately is really tough without a dial indicator.
Did you get any speech chips?
Here are some photos of a recent project that I did:
The finished product:
Hi Mike,
Looks like you’re going about it right! Starting with a manual setup is a wise idea. It gets you a “feel” for the machine! CNC can easily be added later.
I make up a 1:1 printout of the part on my laser printer, then tape it down over the stock to be machined. Then I know when I’m in the proper ball park. But I use the CNC (or your turn count) to get the actual setting; the printout just keeps me safe (usually from the stepped clamps!), and gives me a “sanity” check.
You WILL make scrap parts! That’s part of the learning process. But try cheap material first, vs. big pieces or expensive pieces of stock! Thin plywood can be cut on as well; I do that when I make big parts like flywheels or bases.
May the SWARF be with you!
Alan KM6VV